Palletised Cask Filling System
Available Systems
The most common system in use in Scotland is the Caskmaster developed J E Cockanye [8]. The system is a two-stage filler and consists of a short lance with two pressure tapings at different distances from the lance end, this assembly is known as a filling head. The lance is lowered into the cask and the filling process commenced by an operator, the systems fills the cask initially at its maximum flow rate; the fast fill stage, approximately 300 litres per minute (0.005m3/s). When the lower pressure tapping becomes immersed the system slows the fill rate to less than 60 litres per minute (0.001m3/s); the slow fill stage. Filling is completed when the second pressure tapping becomes immersed. The immersion causes a pressure change at the taping, the change is detected by differential pressure sensors located in a control cabinet remote to the filling head, this requires several meters of tubing to connect the point of measurement to the sensors, the pressure change due to immersion is of the tapings is approximately 5mPa. The transmission of this analogue pressure signal through tubing results in a slow reaction time and small leaks can cause the system to malfunction; overfilling casks and splashing spirit due to an overlong fast fill stage. The pressure tapings can also retain spirit after a fill due to capillary effect which can cause an under fill of the next cask. When the lower taping retains spirit the next fill will not commence and the filling process must be interrupted to allow the issue to be rectified and a zero volume fill is recorded on the logging database. The upper taping retaining spirit leads to the proceeding cask fill being completed immediately after the fast fill stage. This can be more problematic; if the under filling is not noticed by the operator there is potential for several casks to be under filled which is costly due to the resultant warehousing of casked air. Caskmaster filling time is approximately 110s for a hogshead, this time excludes the bunging of the casks, filling head insertion and cask conveying.
The main advantage of the Caskmaster is the pneumatic logic control which is safe for use in explosive atmospheres, however this was a more distinct advantage when such equipment was not widely produced however the extension of ATEX legislation [9] which increased the areas required to use explosive atmosphere rated equipment has led to industrial measuring and control equipment providers such as Siemens and Endress + Hausser offering ATEX approved configurations the majority of instrumentation [10][11].Within Diageo Maturation there are 8 Caskmaster filling systems installed such as at Blythswood in the picture below.
There is a similar two stage filling system developed by Briggs of Burton at Diageo Leven. The only significant difference is the transition from fast fill to slow fill is dictated volumetrically not a pressure taping, this allows a higher fast fill rate due to the increased accuracy and faster response of the digital flow meter compared to analogue pressure sensors. Fill completion is still dictated by a pressure taping.
Diageo has one palletised filling system at Menstrie Bond, Alloa; shown below. The system is a Caskmaster with slightly extended lances and the lifting mechanism modified to suit the vertical lift operation. The main additional limitation is the large distance between cask end and the filling nozzle when the fill begins which results in foaming of the spirit, the foam can lead to false triggering of the fill level sensors or exit the cask as the spirit level rises. Menstrie is predominantly utilised for filling rum which is aged for three months as opposed to the three year minimum for whisky which means maximising the fill level is less crucial.
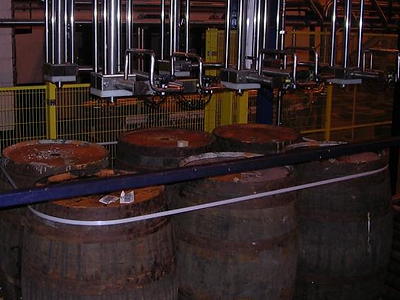